Ramiona RW-200N kombajnu KSW-460NE zostały, jako pierwsze, wyposażone w doświadczalną instalację zewnętrznego zraszania powietrzno-wodnego w ramach realizacji projektu celowego nr 6T12 2004C/06337 dofinansowanego przez Ministerstwo Edukacji i Nauki. Instalacja ta przeznaczona jest do zapobiegania zapłonowi metanu i zwalczania zapylenia w warunkach zagrożenia metanowego.
Instalacja składa się z dysz dwuczynnikowych, przewodów doprowadzających oraz aparatury kontrolno-sterującej.
Doprowadzana do kombajnu woda oraz sprężone powietrze, po zredukowaniu ciśnienia do wartości 3-5 bar, są dostarczane osobnymi przewodami do dysz dwuczynnikowych, gdzie następuje ich mieszanie i wyrzucanie na zewnątrz w postaci mgły powietrzno-wodnej.
Zainstalowana w kombajnie instalacja powietrzno-wodna w znacznym stopniu ogranicza zużycie wody zraszającej, a przeprowadzone badania w Kopalni Doświadczalnej „Barbara” wykazały jej dużą przydatność w gaszeniu płomieni gazowych i zapobieganiu ich powstawaniu. Woda rozpylona do postaci mgły jest również skutecznym narzędziem do ograniczenia zapylenia w ścianie.
Instalacja powietrzno-wodna umożliwia również zraszanie wewnętrzne (przez organ) mieszaniną powietrzno-wodną. Mieszanina ta tworzona jest w specjalnym mieszalniku, umieszczonym w ramieniu kombajnu.
Każde z ramion kombajnu jest wyposażone w kilka do kilkunastu dysz powietrzno-wodnych. Niskie ciśnienie wody zasilającej (maks. 5 bar) i zużycie wody zraszającej (maks. do 100 l/min na cały kombajn) nie wymaga stosowania pompy podnoszącej ciśnienie, a woda do zasilania instalacji zraszającej kombajnu może być pobierana bezpośrednio z rurociągu p.poż..
Instalacja zraszająca, powietrzno-wodna może być zabudowana równolegle z klasyczną instalacją wodną, co umożliwia korzystanie, w zależności od potrzeb, z jednej lub drugiej instalacji.
Pierwszy kombajn typu KSW-460 NE z powietrzno-wodną instalacją zraszającą rozpoczął eksploatację w KWK „Pniówek”.
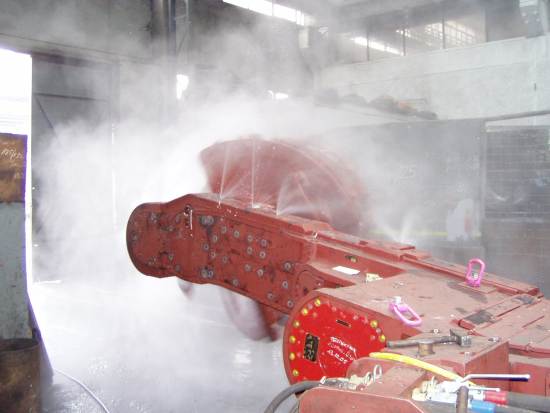
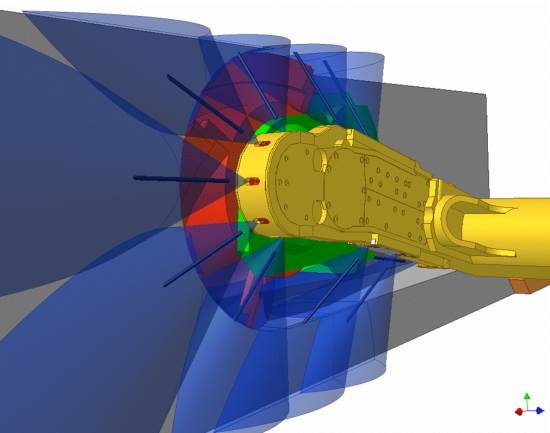